top of page
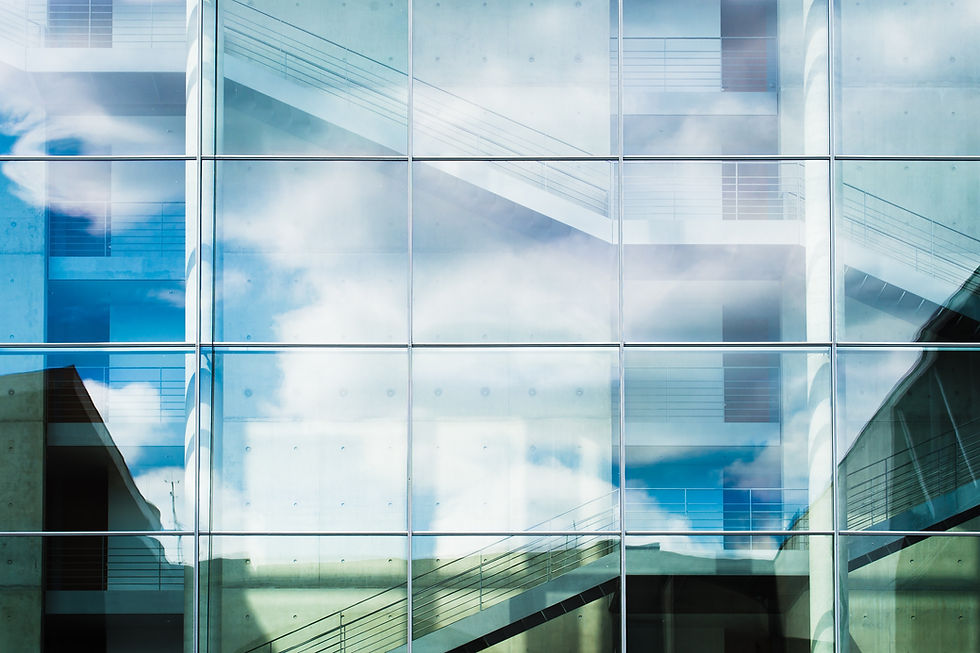
CERM-EX COLD-FORMED STEEL STRUCTURES
​
Our cold-formed steel profiles are used for all types of construction projects. We design different sizes and thickness of steel profiles. All our projects are produced according to precise specifications.
- Cold-formed profiles
- Custom-made production
- Profiles available in different widths: from 75 mm to 250 mm.
- Steel gauge: 0.70 - 2.00 mm
- Excellent protection against corrosion.
Advantage of Cold-Steel Framing
Cold -formed steel framing technology, also known under the name of light steel framing structures, is a construction technique that i already widely used in numerous countries. This method undoubtedly as many advantages.

Sustainability
​
A considered and sustainable choice for the generations to come.
Accuracy
​
The profile sections are made within an accuracy of 0.1 mm.
Strength
​
Light gauge steel material is used to give the highest resistant/weight ratio in the world
Lightness
​
CERM-EX offers a light gauge construction solutions.
Quick
​
A light steel framework gives a significant time-saving on site.
Who are CERM-EX's frame aimed at?
Private Customer
Are you looking for a sustainable construction method?
Choose light steel framing from CERM-EX.
​
You are already working with a contractor/architect:
Ask them to contact us in order to discuss particulars with us.
​
You don't have a contractor/ architect yet:
We can put you in contact with one of our partners in your region.
​
Contractors
We supply our steel frames to contractors and construction companies. We send requests for information from private customers regarding construction project to our partners.
​
Would you like to become our partner?
Please contact us for more information.
​
Architect
- Design and drawings

- Stability study
- Light steel framing production

Construction
Project
Contractor
- Erection on site and cladding
Modular Lightweight Steel Construction
Time Saving – Reduced Overall Construction Time
Construction of modular buildings takes place simultaneously with the site works, allowing projects to be completed earlier.
​
Since the production of modular buildings can happen simultaneously with the site foundation works and the assembly is much faster than in traditional construction, projects can be completed from 50% to 60% faster than in cases of on–site construction. Furthermore, since a significant portion of the construction is completed inside a factory, which mitigates the risk of weather delays from 60% to 90%.
Buildings are completed earlier, occupied sooner and create a faster return on investment.
​
Overall Cost Savings
The use of prefabrication construction methodology allows cost savings at every phase of the production process due to mass production. For example: material savings at the procurement stage and labor savings at the construction phase additional savings can be associated with installation efficiencies and the standardization of the spaces. Shorter construction time inducing lower overhead costs, earlier opening of the new facility generating higher rate of return on investment (ROI) and systematic production under strict QCQA, hence reduced lost material and higher efficiency are all important parameters in the overall cost savings which are induced by using the prefabricated modular construction systems.
​
Minimizing Environmental Impact of the Construction Process
Protecting the health of the patients is one of the biggest challenges to hospitals and other healthcare facilities during construction. Any construction project, no matter how well managed it is, will create at least some dust and debris. While this would not present a problem in most construction sites, in a hospital, dust and debris can be life-threatening if not handled properly.
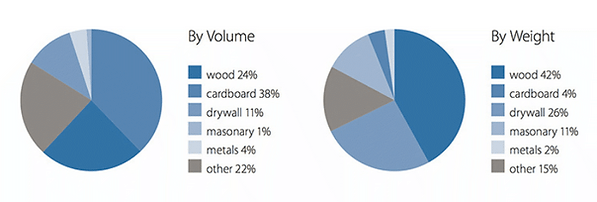
Construction Waste
Removing approximately 80% of the building construction activity from the site location significantly reduces site disruption, noise pollution, air pollution, and also infection risks (infection control will be the most important consideration when it comes to hospital construction projects).
Thence, for any active businesses, reducing on-site construction activity and thereby eliminating a large part of the ongoing construction hazards, is a tremendous advantage.
As owners and designers look for more sustainable designs for improved environmental impact, modular construction is inherently a natural fit. Building in a controlled environment reduces waste. Waste is eliminated by recycling materials, controlling inventory and protecting building materials. This, along with improved quality management throughout the construction process and significantly less on-site activity and disturbance, promotes sustainability. Based on this evidence, the contribution of the modular prefabricated construction system achieves “Green Building”.
​
Safer Construction Environment
Safety remains a major concern for the construction management. Construction by nature has a high degree of hazardous activities. The price of construction accidents is high in terms of both costs and suffer.
​
Accidents add a burden of needless and avoidable expense. Direct costs include medical costs and compensation. Indirect hidden costs include:
-
Time lost from work by the injured party
-
Loss in earning power, economic loss to injured worker’s family
-
Loss of efficiency by breaking up crew
-
Cost to train new or replacement employees
-
Damage to equipment and tools
-
Loss of production
-
Cost incurred by delays
-
Overhead costs associated with disruption of work
-
Clean up and repair costs
-
Administrative costs of investigations and reports
-
Increased insurance premiums
-
Loss of future projects due to adverse publicity
-
Cost of fines
​
The indoor construction environment reduces the risks of accidents for workers as well as provides improved on–site working conditions, less noise and air pollution, less on–site traffic, turns the working zone into a safer environment with lower risks. Thus giving additional value to the contractor cannot be neglected.
​
Greater Flexibility and Reuse–Presenting a Relocatable Modular Building
Another advantage of the special prefabricated modules is their ease of relocation when the need arises, reducing the demand for raw materials and minimizing the amount of energy expended to erect a building to meet the new need.
A Relocatable Building is a partially or completely assembled building that complies with applicable codes and regulations and is constructed in a building manufacturing facility using a modular construction process.
​
Relocatable modular buildings are designed to be reused or repurposed multiple times and transported to different building sites.
​
Relocatable modular buildings are utilized mainly for medical clinics and to any application where a relocatable building can meet a temporary space need. These buildings offer fast delivery, ease of relocation, low-cost reconfiguration, accelerated depreciation schedules and enormous flexibility. These buildings are essential in cases where speed, temporary space and the ability to relocate is necessary.

Up to 70% shorter construction time

Investment security

Ecology and sustainability

Energy efficiency

Appealing architectural design

Clean and quiet construction sites
bottom of page